Blog
Common Maintenance Practices for Shearing Machines:
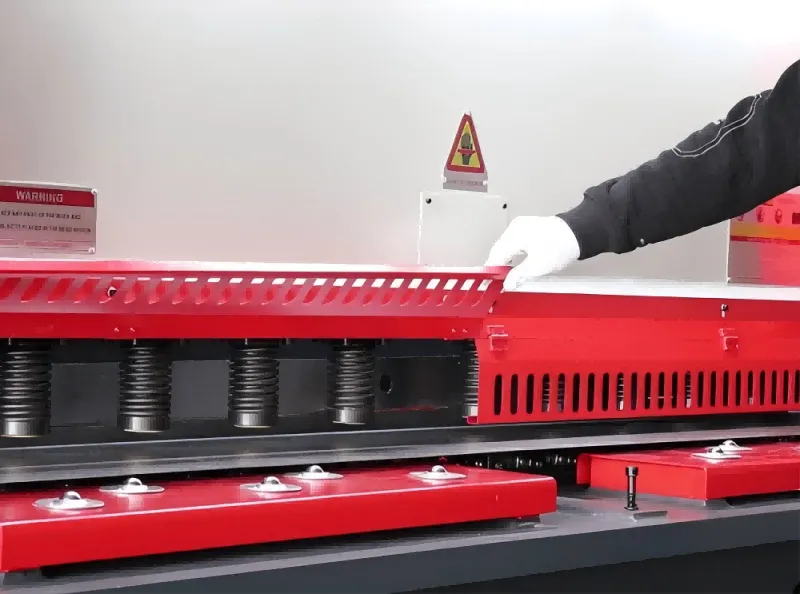
Shearing machines are vital in metal fabrication and manufacturing. They cut metal sheets quickly and accurately. To ensure their long-term performance and accuracy, regular maintenance is essential.
Whether your CNC shearing machine is manual, mechanical, or hydraulic, regular maintenance saves you time and money. It also helps to prevent unexpected downtime.
When you buy hydraulic CNC shearing machine factory like Miharmle, pick a quality machine. Also, commit to keeping it well maintained. Let’s explore the best maintenance routines. These will help your shearing machine last longer and work better.
1. Daily Inspection and Cleaning:
Check your shearing machine every day. Clean it on a regular basis. This keeps it in good shape. Before starting the machine each day:- Check for any visible signs of wear or damage on the blades, hold-downs, and back gauge.
- Wipe down all accessible surfaces to remove metal shavings, dust, and oil residue.
- Ensure all safety guards and emergency stops are functional and properly in place.
2. Lubrication:
You should never overlook lubrication, as it is a vital maintenance task. It minimizes friction between moving parts and helps prevent premature wear. Depending on your machine type, lubrication points may include:- Guide rails
- Bearings
- Cylinders
- Slideways
3. Blade Maintenance and Sharpening:
Blades are key to a shearing machine. Their condition affects cut quality directly. Dull or chipped blades hurt the workpiece’s finish. They also put extra strain on the motor and hydraulic system. Best practices include:- Checking blade clearance daily.
- Rotating or flipping blades is a double-edged sword.
- Scheduling periodic sharpening depending on usage volume.
4. Hydraulic System Care:
For hydraulic shearing machines, the hydraulic system must be monitored closely. A failure here can bring production to a complete stop. Key maintenance tasks include:- Checking hydraulic oil levels weekly.
- Replace the hydraulic oil every 6 to 12 months, or as recommended.
- Inspecting hoses and connectors for leaks or cracks.
- Cleaning or replacing hydraulic filters as needed.
5. Backgauge Calibration:
The backgauge ensures accurate and consistent cut lengths. It should be inspected and calibrated to avoid costly material waste. Operators should:- Verify the back gauge position against a standard measuring tool.
- Tighten any loose bolts or misalignments.
- Check for mechanical wear in gears and drive mechanisms.
6. Electrical Components and Control Panel:
The control panel is the brain of the machine. Keeping it in good condition ensures smooth operation and reliable performance. You should:- Inspect the wiring and terminals for signs of wear or overheating.
- Test the limit switches and sensors.
- Check the CNC system for software updates or bugs.
- Clean the panel with dry air or an antistatic cloth to avoid dust buildup.
7. Fastener and Alignment Checks:
Check bolts, nuts, and machine alignments monthly. Vibrations and heavy use can gradually loosen fasteners or misalign critical components. Failure to address these issues can result in poor-quality cuts or mechanical failure.- Use a torque wrench to retighten key bolts.
- Align blades and squaring arms to the machine’s table.
- Check for vibrations during operation and identify their source.
8. Operator Training and Record Keeping:
Even the most well-maintained machines can suffer if operated improperly. Invest in proper training for all machine operators to ensure they:- Understand safety protocols.
- Follow startup and shutdown procedures.
- Know how to recognize signs of mechanical stress or failure.