Business
Effective Techniques for Estimating Material Costs in Construction
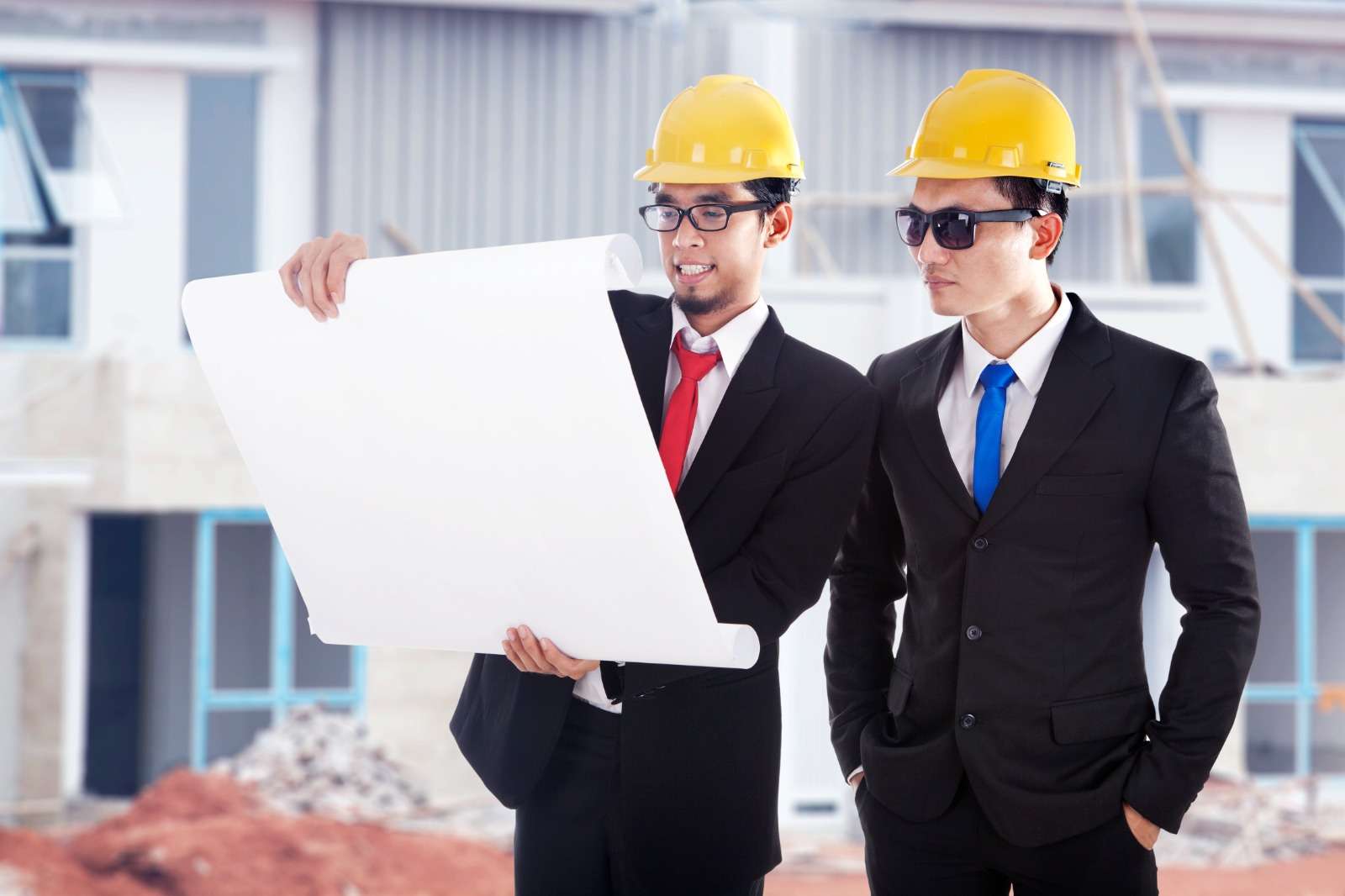
Cost estimation for materials is just as important as being able to continuously bid on the construction projects and to bring in profit to the company. But it should be noted that such material cost may vary enormously and can change over the time of a particular project and it will be difficult for you to predict. Here is an article that guides the readers to some key and effective techniques construction estimators can use to improve the precision of their material cost estimations.
Analyze The Propositions From Several Contractors
It is recommended to use the vendors who provide the quotation directly to get the estimated cost of materials. Make sure they provide you with quotes from at least three vendors for each major trade and material; then, you will be able to compare prices. Note that the quoted prices from the vendors will frequently be the discounted price for the bigger orders, so you will need to make modifications if your project specifications change. The process of asking several counts gives you the chance to do comparisons with the industry standard prices and you end up with a backup data source if the first vendor quoted you a building price that is in contrast with the industry rate.
Leverage Historical Data
The meaning of looking at the expenses you have incurred on the materials for the previous projects that are stake sizes and scopes in your company form an excellent base for roofing estimating services. Your estimator could refer to the records of actual cost and okay to many boxes and compare them with the current project’s qualifications. This entails your firm applying the actual materials cost method; it thus involves your firm tracking and recording expenditure by project. If the data within the historical systems are not available, averages of construction cost per square foot provided on the national databases can provide a reasonable check.
Account for Price Fluctuations
The historical prices and cheapest offers can only represent particular points in time. More substantial structures with longer timeframes may face material changes considerably throughout the construction takeoff services. Look into movements in commodity prices during the project life cycle period, and incorporate the expected surplus or further costs before the final budget. Volatility spikes occur when the validity period of the bid is shorter, by adopting escalation clauses or commodity futures contracts a risk manager can mitigate the risks of unexpected price hikes.
Get Contractor Input
A great roof replacement cost estimator assumes that the construction process and the techniques are taken into account as they influence the quantity of the material. Sit down with the contractors to analyze the construction sequence and see what specifications they want for the project. The contractor’s technique and method are often reflective of the scope and quantity of materials. For instance, their formation determines the amount of concrete and rebar for foundations and slabs; the conditions of a structure and the soil conditions determine the amount of concrete and rebar for foundations and slabs. As the final step, obtain the calculations input from the given build strategy before finalizing the estimated quantities.
Compute The Amount Over & The Amount Short
See to it that your estimates take into account leftover overstock, and cost reserve for these. Use waste factor or overage as a multiplier to calculate material quantities before applying the cost factor. Used materials usually start from around 5-20% of the given material depending on its kind. Taking into account the rates of usage, the dimensions and options of the site as well as the complexity level of the project, you should determine the volume of waste generated. With a 5% margin, the non-stocked products of overordering can handle damaged merchandise and manufacturer waste. This allowance amount should be increased to prevent the extended lead items from being non-returnable.
Validate with Third-party Resources
Thanks to the quotes and historical data, these consultants have a great vital point to start with, so it will be an excellent idea to make a reasonability check using the databases inside the company or to get the help of third-party cost databases. Several estimators resort to RSMeans and Gordian’s CostWorks which compile average material market prices for comparison. For instance: A range of estimators subscribe to the services of RSMeans and Gordian’s CostWorks which include the summarized data on material market prices. Ask them to align their materials cost figures to their construction project cost data by square feet if that is your project type. If you need to have a very detailed model, you can try and compare at the line item level.
Conclusion
The cost-estimating process for construction companies is both an art and a science. As said, red tape is not an exact science, but the tips for a performance calculation should set your organization on a good footing Through collecting several vendor quotes, reviewing previous spending records, receiving contractor input, and opening the estimates for external sources review provides for a quality, defensible level of the estimate. Coming up with the most accurate estimates involves the use of strong assessing techniques, thus ensuring your business arrives at the right bid and manages to maintain the necessary profit margin during the projects.