Technology
Enhancing Product Design for Die Casting and Plastic Molding
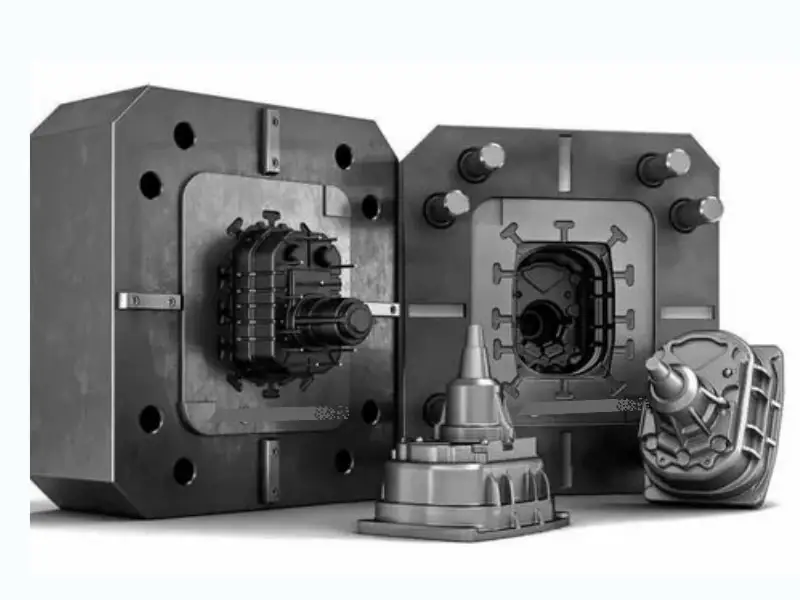
In the realm of assembling, Die Casting Mold and plastic Mold are two central cycles that are broadly utilized for making complex parts with high accuracy. As organizations push for proficiency and cost-viability, upgrading item plans for these cycles has become more urgent than any other time in recent memory. A very much upgraded plan lessens creation costs as well as guarantees a smoother fabricating process, eventually prompting better item quality.
Understanding Die Casting Mold and Plastic Mold
Prior to plunging into streamlining methodologies, it’s fundamental to have a strong handle of what Die Casting Mold and plastic Mold involve.
What is Die Casting Mold?
Die Casting Mold is an assembling interaction where liquid metal, typically a composite like aluminum or zinc, is infused into a shape cavity under high tension. This strategy is known for creating exact, complex metal parts at high volumes with incredible surface completions and layered precision.
What is Plastic Mold ?
Plastic Mold, then again, includes softening plastic pellets and infusing them into a shape to frame a section. Different strategies like infusion forming, blow shaping, and thermoforming fall under this class, each offering special advantages relying upon the application.
While Die Casting Mold is in many cases picked for metal parts, plastic Mold rules ventures like car, hardware, and purchaser merchandise because of its flexibility and cost-adequacy.
Key Contemplations in Item Plan for Die Casting Mold
Planning for Die Casting Mold requires cautious meticulousness, as the interaction is profoundly delicate to specific plan boundaries. Here are a few fundamental contemplations:
1. Wall Thickness
In Die Casting Mold, uniform wall thickness is essential for keeping away from surrenders like porosity and twisting. Dainty walls cool quicker and are inclined to issues, while unnecessarily thick walls increment process durations and material expenses. It is vital for Work out some kind of harmony.
2. Draft Points
To work with simple discharge of the cast part from the bite the dust, consolidating draft points is important. Normally, a draft point of 1 to 3 degrees is suggested, contingent upon the profundity of the part.
3. Filets and Ribs
Sharp corners can prompt pressure focuses and breaks in the eventual outcome. Supplanting them with filets reinforces the part as well as works on material stream during projecting. Additionally, adding ribs can upgrade primary trustworthiness without expanding wall thickness.
4. Undermines and Ejector Pins
Undermines ought to be limited or dispensed with as they convolute the bite the dust plan and increment creation costs. Ejector pins ought to be decisively put to try not to leave blemishes on basic surfaces.
5. Resistances and Surface Completions
Bite the dust projecting offers high accuracy, yet architects should determine practical resiliences to adjust cost and usefulness. Also, choosing fitting surface completions is crucial for the two feel and execution, particularly in parts presented to cruel conditions.
Key Contemplations in Item Plan for Plastic Mold
With regards to plastic Mold, the adaptability of configuration is one of the cycle’s most grounded places. In any case, explicit rules ought to in any case be kept to guarantee an effective result.
1. Material Choice
It is basic to Pick the right plastic material. Factors like strength, adaptability, warm obstruction, and cost ought to direct your choice. For instance, ABS offers great sturdiness, while polycarbonate succeeds in influence obstruction.
2. Wall Thickness Consistency
Very much like in Die Casting Mold, uniform wall thickness is critical in plastic trim to forestall deformities, for example, sink checks and voids. Preferably, wall thickness ought to be kept as flimsy as conceivable without compromising the part’s solidarity.
3. Draft Points
In plastic Mold , draft points help in the smooth discharge of the part from the shape. A draft point of 1.5 to 2 degrees is frequently suggested, yet this can differ in view of the intricacy of the plan and the material utilized.
4. Supervisors and Ribs
Adding managers and ribs can upgrade the underlying strength of the formed part without adding huge weight. Supervisors are usually utilized for mounting screws, while ribs give support in enormous, level segments.
5. Door Position
Door position in plastic molds is imperative for controlling the progression of the liquid plastic. Inadequately situated entryways can prompt air traps and fragmented fills. Architects ought to work intimately with shape designers to upgrade entryway areas.
Enhancement Procedures for The two Cycles
While Die Casting Mold and plastic Mold have their extraordinary plan contemplations, some advancement procedures apply to the two cycles.
1. Utilization of Reenactment Devices
Present day computer aided design programming and reproduction devices permit fashioners to anticipate likely issues in the projecting or forming process. By reproducing material stream, cooling rates, and stress dissemination, creators can improve their items before genuine creation, saving time and expenses.
2. Prototyping and Testing
Making models and leading thorough testing is a significant stage in the enhancement cycle. Fast prototyping procedures like 3D printing take into account speedy emphasess and refinements prior to moving to full-scale creation.
3. Joint effort with Makers
Close joint effort with makers during the plan stage guarantees that the plan is manufacturable and lines up with the abilities of the picked interaction. Ordinary correspondence can assist with distinguishing potential difficulties early and stay away from exorbitant overhauls.
4. Cost Enhancement
Streamlining a plan for assembling isn’t just about further developing execution yet additionally about diminishing expenses. By limiting material utilization, improving on the plan, and choosing financially savvy materials, creators can fundamentally decrease in general creation costs without forfeiting quality.
End
Upgrading item plan for Die Casting Mold and plastic Mold is a complex however compensating task. By zeroing in on the critical contemplations and utilizing current apparatuses and procedures, organizations can accomplish superior grade, practical items that satisfy the needs of the present cutthroat market.