Business
How to Combat Food and Beverage Warehouse Challenges
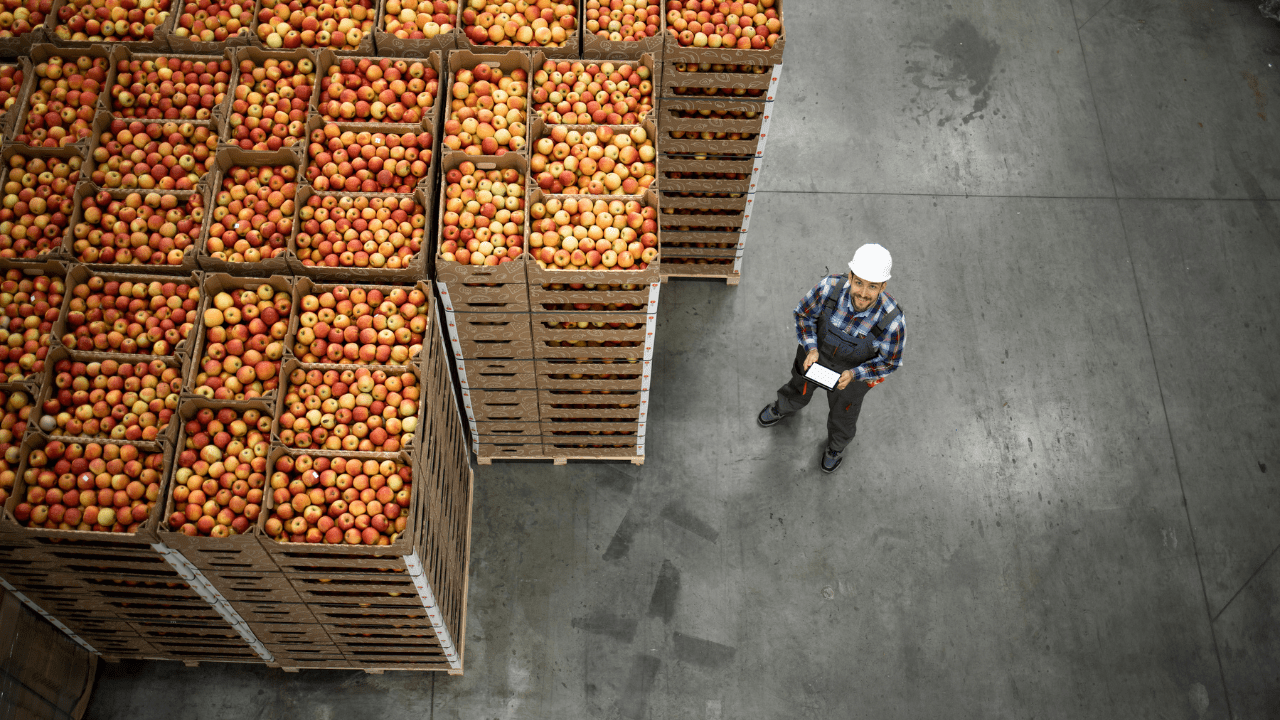
We’re all faced with issues related to supply chain shortages, especially in the past few years. Companies frequently have to scramble to get ingredients from various suppliers. Businesses are dealing with new suppliers or attempting substitutions that will satisfy their savvy customers. Managers often wonder if there is a better way to handle these challenges so they can provide the best experience for customers.
The greatest solution to combating all these difficulties is creating a plan that allows for pivoting, investing in the technology and resources to see the plan through, and educating staff to move quickly and effectively though these challenges.
A Plan
First, warehouse managers need a plan. This would likely include inventory management systems, software or apps, scanning systems, and other tools to make inventory data collection a breeze to implement. Knowing any weak points to a warehouse supply chain allows a warehouse manager to meet those challenges head on.
A good plan also includes appropriate warehousing and distribution layout. If employees don’t know where to put inventory or the warehouse design is not intuitive, how will they know what has been scanned and what needs to be added to inventory? How will they be able to find products when orders arrive? How will they know if an item is returned and resaleable or not? These questions must be answered quickly by means of a warehouse utilizing the appropriate layout to maximize efficiency in all areas — including pick-pack-ship and returns.
A Pivot
Another aspect of a good plan is a pivot. If a business typically orders cream from supplier A, and supplier A cannot provide that cream due to a Listeria outbreak, then what is the business to do? Smart businesses will be prepared to pivot to Supplier B, or C, or even D to make sure that the cream they need for their product or to ship directly to their customers is available.
If Supplier B’s cream formula is slightly different than Supplier A’s, other adjustments in the formula may need to be made. Some substitutions are acceptable to some customers. Other times, no substitutions will be accepted. If multiple suppliers cannot be found to supply whatever ingredients or products are needed, then warehouses must have a plan to keep their customers happy. Perhaps that’s presenting a new flavor. Maybe it’s offering a discount or a rain check.
Many supply chain problems can be overcome simply by better pre-planning of orders. Let’s say that successful businesses present their orders for the holiday rush by June, but a struggling business waits until September. They know they don’t have the appropriate cold-storage facility to house a large order, so there is a high probability that the supplier will be out of stock by the time that struggling business even places their order. These kinds of supply chain issues can further limit an already struggling business.
Assess Weak Areas
Next, warehouse managers need to assess weak points in their warehouse layouts and identify solutions. One way to accommodate placing an order sooner is by renting extra cold storage facilities. Renting this additional cold storage solutions facility temporarily would allow a manager to gauge the higher demand of a product before committing to building an entirely new warehouse. In other situations, a product needs to be moved just for a short time so that a better layout can be created without catastrophic interruption of order processing.
To know if extra storage is the right move for a warehouse business, a thorough and thoughtful assessment of the current layout, inventory management, staff, and warehouse processes is in order. Investing in the inventory management tools and listening to concerns raised by staff, including close calls and incident reports, will help warehouse managers know if their inventory has simply outgrown their space. Then, effective managers can utilize a pivot that will work for their business.
Address Staffing Concerns
Staffing is always a challenge in warehouses, where turnover can be very high. Education and training of new staff to be fast, efficient, and safe can be a considerable challenge. But investing in people, giving them the tools they need to be effective workers, listening to their concerns and their suggestions, can turn a high turnover workforce into a loyal workforce that stays and grows the business.
Imagine how much money could be saved if employee training could be greatly reduced. Or, consider how much speed could be improved if veteran employees weren’t spending so much time filling in the gaps of a new hire’s training. Often warehouse managers see a seasonal peak and think their business is booming, so they need to hire more staff, they need a bigger warehouse, they need to shift their focus. However, when the peak passes, and so does some of their business, employees are laid off, business may be shuttered, and everyone is unhappy. Managers may be able to curb this effect with healthy growth options such as temporary storage solutions and flexible training options.
When the staff knows the procedures and is comfortable with them, product orders get filled quickly and accurately. Investing in the tools to help staff be successful is always a smart decision. Seeing an effective warehouse layout makes it easier to train employees to recognize a plan and carry it out. This also helps avoid warehouse bottlenecks which can delay picking, cause confusion, and even cause workplace injury.
Even if staff turnover is high, a good plan makes it easy to train new hires and solid training up front will help experienced staff spend more time picking and less time re-training or babysitting the new hires. If the warehouse is making use of zones, staff may not need to know everything about every zone, but may become experts of the smaller area where they will spend most of their working hours. More experienced staff can be cross-trained to cover areas that need it and coordinate with others in the warehouse. Throwing too much information to a new hire at once might be inefficient and a waste of everyone’s time.
Final Thoughts
Tools exist to help managers make the best decisions for the warehouse’s prime efficiency. Allow them to be used in the best ways. Empower staff to contribute their observations, criticisms, suggestions, and solutions, and make use of temporary storage as needed. With a great plan in place, warehouse managers can combat any food or beverage challenge that may present itself. For more information about options in multi-temperature storage, please contact Refrig-It Warehouses for a quote.
Refrig-It is a leader in multi-temperature storage, with options for all types of food and beverage manufacturers. Its two New Jersey locations are adjacent to New York City and offer premium chain logistics new jersey to importers and distributors of food products.