Uncategorized
Tips for Maximizing Efficiency in Plastic Extrusion
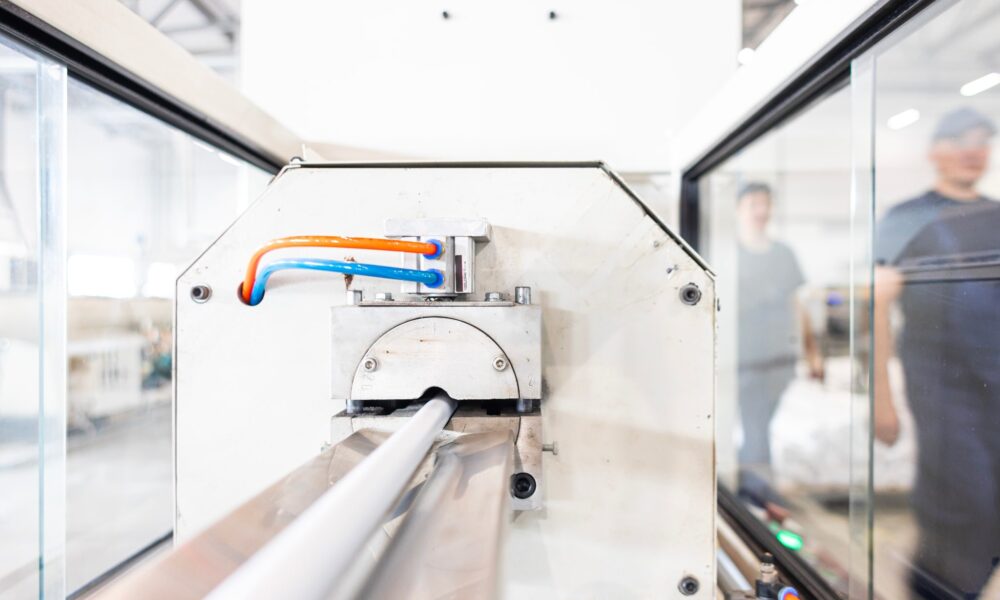
Plastic extrusion shapes materials into custom profiles used in automotive trims, solar panel frames, and appliance tubing. Plastic manufacturers work with single screw extrusion systems for simple resins or twin-screw machines for filled compounds. High-quality equipment helps manufacturers improve efficiency when producing large orders or precision parts. Here are some ways to maximize efficiency in plastic extrusion processes:
Adopt Automation
Automation in plastic extrusion boosts consistency, speed, and repeatability across various production runs. When your production line uses automated equipment, such as servo-driven pullers, you achieve precise tension. Automated in-line cutters produce accurate lengths without slowing output for volume targets. Closed-loop systems track and adjust your settings in real time to reduce errors and waste materials.
Auto-load feeders simplify your workflow and result in consistent resin mixes that meet specific product demands. If you produce dual-hardness profiles, automated feed changes let you switch materials without stopping your line. This prevents delays in the production of parts like automotive trims or weather seals.
Refine Temperature Control
Proper temperature control allows manufacturers to achieve even thickness in extruded plastic products. The right temperature determines the quality of your output by keeping the plastic in a molten state until it’s ready to be formed. Consistent temperature control helps you achieve uniformity in your material, and it prevents plastics from warping and bubbling.
Keeping a record of temperature readings allows you to identify patterns that may affect production. Changes in a plastic part’s durability could be a sign of temperature fluctuations during production. If your extruded parts are cracked, low temperatures could be to blame. High temperatures increase the risk of bending during processing and product formation.
Monitor Melt Pressure
Monitoring melt pressure can help you detect early signs of inconsistent flow and prevent compromised part strength and appearance. Steady melt pressure keeps output within specification ranges. This is beneficial if your line produces high-tolerance components, like automotive seals or solar panel frames. Integrated pressure sensors let you track extrusion performance in real time, instead of after defects appear. This enables you to make faster manufacturing adjustments and apply tighter quality control standards to achieve fewer rejected runs.
Check Quality Control
Regularly checking your extrusion equipment for performance helps maximize production quality. Routine inspections allow you to identify potential issues before they become significant problems that interrupt operations. During a visual inspection, look for any abnormalities or damage to the equipment. Take note of cracks, dents, or other signs of wear that could affect the quality of your plastic parts. If you find that your equipment has worn dies or fluid leaks, schedule a maintenance service to restore consistent, high-quality output. You can also lubricate your equipment and affirm all bolts and screws are properly tightened before resuming production.
Increase Your Plastic Extrusion Efficiency
Manufacturers in industries like packaging and automotive benefit from plastic extrusion’s versatility. Partnering with a plastic extrusion company allows you to enhance your plastic product designs. These companies can handle high-volume parts orders and offer a variety of plastic materials and custom extrusion dies. This supports creative product designs and helps your product stand out due to its improved performance and greater functional value. Contact an extrusion company today to discuss how they can help you improve your plastic production efficiency.