Technology
What Are the Advantages of Laser Marking?
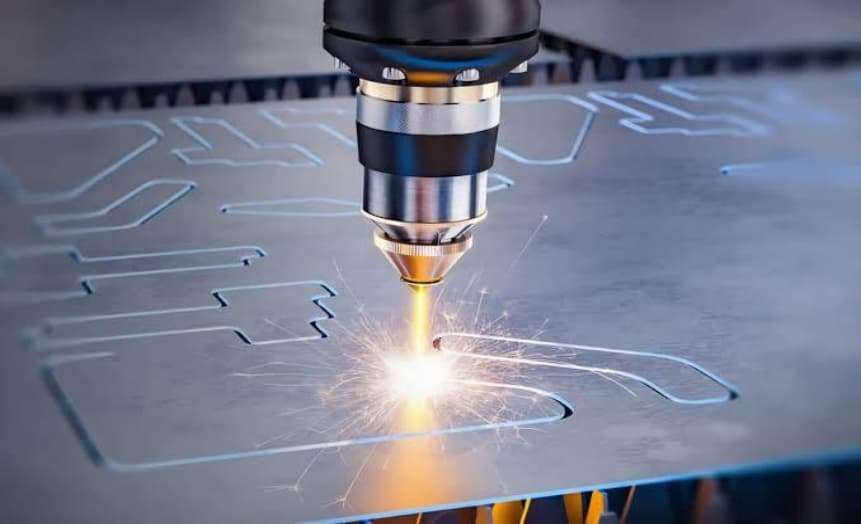
Are you looking for a cutting-edge solution to mark your products with precision and efficiency? Look no further than laser marking! In this blog post, we will explore the advantages of laser marking over traditional methods, its applications in various industries, the types of materials suitable for laser marking, and key factors to consider when choosing a laser marking system. Let’s dive into the world of laser technology and discover why it has become the preferred choice for product identification and customization.
The Process of Laser Marking
Laser marking is a precise and efficient process that involves using a laser beam to create marks on various materials. The process begins by focusing the laser beam onto the surface of the material, causing it to heat up and interact with the material’s properties.
As the laser moves across the surface, it creates high-contrast marks without physically touching or damaging the material. This non-contact method results in clean, permanent markings that are resistant to wear and tear.
Different types of lasers can be used for marking, including fiber lasers, CO2 lasers, and UV lasers. Each type offers unique advantages depending on the specific requirements of the application.
By adjusting parameters such as power density, pulse duration, and wavelength, manufacturers can achieve different mark depths, sizes, and colors. This flexibility makes laser marking suitable for a wide range of industries seeking high-quality markings on their products.
Advantages of Laser Marking over Traditional Methods
Laser marking offers numerous advantages over traditional methods of marking and engraving. One key benefit is the high level of precision it provides, allowing for intricate designs and detailed markings to be achieved with exceptional accuracy.
Compared to conventional techniques such as mechanical engraving or chemical etching, laser marking is a non-contact process. This means that there is no direct contact between the marking tool and the material being marked, reducing the risk of damage or distortion to delicate surfaces.
Another advantage of laser marking is its versatility in terms of markable materials. From metals and plastics to ceramics and glass, laser marking can be applied to a wide range of substrates with consistent quality results.
Furthermore, laser marking is a fast and efficient method that enables high-speed production without compromising on quality. The speed at which lasers can mark materials makes them ideal for industrial applications where productivity is crucial.
Applications of Laser Marking in Different Industries
Laser marking has found versatile applications across various industries, revolutionizing the way products are marked and traced. In the automotive industry, laser marking is used for engraving serial numbers, barcodes, and logos on parts for identification and tracking throughout the supply chain.
In the electronics sector, laser marking ensures permanent branding of components without damaging sensitive materials. This technology is also widely adopted in medical device manufacturing to mark surgical instruments with precise information like lot numbers and expiration dates.
The aerospace industry utilizes laser marking for part serialization, enabling easy maintenance and traceability of critical components. Moreover, in the jewelry industry, lasers create intricate designs on precious metals with unmatched precision.
From consumer goods to industrial equipment, laser marking offers a reliable solution for product labeling that withstands harsh environments while maintaining aesthetic appeal.
Types of Materials Suitable for Laser Marking
When it comes to laser marking, the type of material being marked plays a crucial role in determining the effectiveness and quality of the mark. Various materials can be successfully marked using laser technology, including metals such as stainless steel, aluminum, and titanium. These materials are known for their durability and ability to withstand high heat levels generated during laser marking processes.
Additionally, plastics like ABS, polycarbonate, and PVC are also suitable for laser marking due to their versatility and widespread use in industries ranging from automotive to electronics. Glass is another material that can be effectively marked using lasers, offering a permanent and precise marking solution ideal for applications requiring high precision.
Moreover, organic materials like wood and leather are popular choices for laser marking due to the clean and crisp marks they produce without damaging the integrity of the material. By selecting the right type of material for your laser marking needs, you can ensure optimal results that meet your specific requirements.
Factors to Consider When Choosing a Laser Marking System
When selecting a laser marking system, it’s crucial to consider the type of material you will be working with. Different materials require specific laser settings for optimal results. Factors like hardness, color, and composition can impact the effectiveness of the marking process.
Another key factor to keep in mind is the desired speed and precision of the markings. Some applications may require fast processing speeds while others prioritize intricate details. Understanding your project requirements will help determine the suitable laser system for your needs.
Consider the size and shape of the items being marked as well. The workspace dimensions of the laser machine should accommodate your products comfortably to ensure efficient production.
Additionally, assess any future scalability needs. Investing in a laser marking system that can adapt to potential growth or changes in production volume will save time and resources down the line.
Evaluate technical support options from suppliers. Having access to reliable assistance for troubleshooting and maintenance can make a significant difference in minimizing downtime and maximizing productivity.
Conclusion
Laser marking is a versatile and efficient method for permanently marking various materials with precision and accuracy. With its numerous advantages over traditional marking methods, such as durability, speed, and flexibility in design, laser marking has become an indispensable tool in many industries.
From automotive to medical devices, electronics to aerospace, laser marking finds applications across a wide range of sectors due to its superior performance and quality. The ability to mark on different materials like metals, plastics, ceramics, and more further enhances the versatility of laser marking systems.
When choosing a laser marking system for your specific needs, consider factors such as the type of material you will be working with, desired marking quality, and speed requirements. By selecting the right system tailored to your requirements, you can maximize efficiency and achieve high-quality results consistently.
In conclusion
Laser marking offers unparalleled advantages that make it a preferred choice for businesses looking for durable and precise markings on their products. Its application versatility combined with superior performance makes it an essential technology for modern manufacturing processes. Incorporating laser marking into your production line can lead to increased productivity, improved product traceability,
and enhanced brand recognition – ultimately helping your business stay competitive in today’s fast-paced market landscape.
Digital Marketing
10 Secrets to Unlocking the Power of SSIS 816
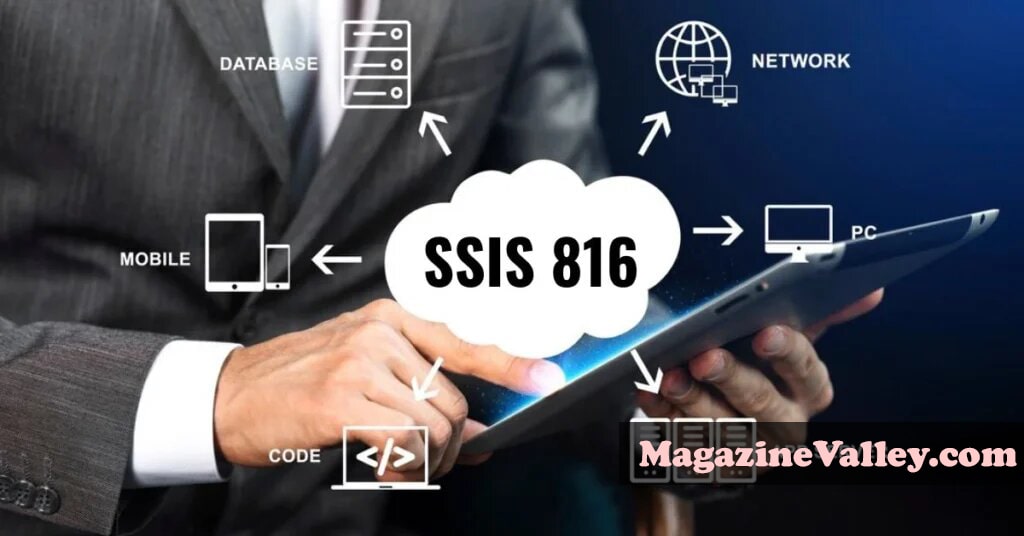
Are you looking to unleash the full potential of SSIS 816 and take your data integration skills to the next level? Look no further! In this blog post, we’ll reveal ten secrets that will help you unlock the power of SSIS 816 like never before. Get ready to streamline your processes, boost efficiency, and supercharge your data management capabilities. Let’s dive in and discover how you can become an SSIS wizard!
Introduction to SSIS 816
Welcome to the ultimate guide to unlocking the power of SSIS 816! In the fast-paced world of data integration, SSIS (SQL Server Integration Services) 816 stands out as a powerhouse tool for streamlining ETL processes. If you’re ready to take your data integration game to the next level and harness the full potential of SSIS 816, you’ve come to the right place. Let’s dive in and uncover the secrets that will empower you to maximize the capabilities of this cutting-edge technology.
Understanding ETL and its Importance in Data Integration
Data integration is crucial in today’s business landscape, allowing organizations to combine data from various sources into a unified view. ETL (Extract, Transform, Load) is a crucial process within data integration that involves extracting data from source systems, transforming it into a consistent format, and loading it into a target database.
ETL is essential for ensuring the accuracy and consistency of data across different systems. Organizations can make informed decisions based on reliable information by standardizing and cleansing data during the transformation stage.
Efficient ETL processes enable businesses to streamline operations, improve decision-making, and enhance overall productivity. With the increasing volume and complexity of data generated daily, robust ETL capabilities are critical for maintaining competitive advantage in today’s digital age.
Evolution of Data Integration Tools: From DTS to SSIS 816
Data integration tools have evolved over the years, evolving to meet businesses’ growing demands for efficient data processing. One significant milestone in this evolution is the transition from Data Transformation Services (DTS) to SQL Server Integration Services (SSIS) 816.
DTS, introduced with SQL Server 7.0, was a game-changer in its time, offering basic ETL capabilities for moving and transforming data within SQL Server databases. However, as technology advanced and data volumes exploded, the need for more robust and scalable solutions became apparent.
Enter SSIS 816 – Microsoft’s powerful ETL tool revolutionized data integration with its flexible architecture, rich transformations, and extensive connectivity options. With features like parallel processing, package deployment utilities, and enhanced logging capabilities,
SSIS 816 has become the go-to solution for organizations looking to streamline their data workflows and drive better decision-making processes by seamlessly integrating disparate data sources. As technologies continue to evolve rapidly in today’s digital landscape,
Key Features of SSIS 816
SSIS 816 is packed with powerful features that make data integration a breeze. One key feature is its robust ETL capabilities, allowing users to seamlessly extract, transform, and load data from various sources. With SSIS 816, users can easily design complex data flow tasks using a visual interface, making manipulating data on the fly simple.
Another standout feature of SSIS 816 is its connectivity options – whether you’re working with SQL Server databases, Excel spreadsheets, or even cloud services like Azure Blob Storage, SSIS 816 has you covered. The ability to schedule and automate package execution is also a game-changer for streamlining workflows and ensuring timely data processing.
Moreover, SSIS 816 offers advanced logging and error-handling functionalities to help users troubleshoot issues quickly and efficiently. Its rich set of transformation components also empowers users to manipulate data in myriad ways without writing extensive code.
Secrets to Unlocking the Power of SSIS 816:
Some essential secrets can genuinely unlock the full potential of SSIS 816. One secret is to make the most of control flow tasks; these allow you to orchestrate your workflow efficiently. Another secret lies in leveraging data flow components to manipulate and transfer data seamlessly between sources.
Creating dynamic packages with expressions and variables is another powerful feature that can enhance the flexibility and adaptability of your SSIS projects. Additionally, taking advantage of logging and error-handling mechanisms within SSIS can help you troubleshoot issues effectively during execution.
Moreover, utilizing event handlers strategically can further streamline your ETL processes. Harnessing the power of script tasks allows for custom functionality beyond what is available through built-in components. Lastly, optimizing package configurations for performance improvements should not be overlooked when maximizing SSIS capabilities.
Utilizing Control Flow Tasks
When working with SSIS 816, mastering control flow tasks is essential to orchestrate the workflow of your data integration processes. Control flow tasks allow you to define the logical sequence in which different operations will be executed within your package.
By effectively utilizing control flow tasks, you can create a smooth and efficient data pipeline that meets your specific business requirements. Tasks such as Execute SQL Task, File System Task, or Script Task provide flexibility in manipulating and moving your data during ETL processes.
Whether you need to perform conditional branching, looping, or parallel task execution, SSIS 816 offers a wide range of built-in control flow components to help you achieve seamless data integration. Properly utilizing these tasks can automate complex workflows and streamline your data processing operations for optimal performance.
Leveraging Data Flow Components
Leveraging Data Flow Components in SSIS 816 is a game-changer for data integration tasks. These components allow you to efficiently extract, transform, and load data from various sources to destinations. By understanding the different types of data flow components available, you can tailor your package to meet specific requirements.
One key component is the Source Assistant, which simplifies extracting data from sources like databases or flat files. Transformations such as Derived Column and Lookup enable you to manipulate and enrich your data before loading it into the destination.
The Destination Assistant facilitates the seamless loading of transformed data into target systems. In addition, utilizing advanced components like Slowly Changing Dimension can help maintain historical records effectively.
Mastering Data Flow Components equips you with the tools needed to build robust ETL processes within SSIS 816 effortlessly.
Creating Dynamic Packages with Expressions and Variables
Creating dynamic packages with expressions and variables is a game-changer when it comes to maximizing the power of SSIS 816. You can adapt your packages to changing conditions without manual intervention by incorporating expressions. This flexibility streamlines your data integration process and enhances efficiency.
Utilizing variables allows you to store values that can be used throughout your package, enabling dynamic decision-making based on changing parameters. This feature adds a layer of intelligence to your packages, making them more responsive to real-time data variations.
Combining expressions and variables in SSIS 816 will unlock the potential for automation and customization within your data integration workflows. This seamless integration empowers you to create robust solutions that meet the evolving demands of modern business environments.
Taking Advantage of Logging and Error Handling
One of the secrets to unlocking the power of SSIS 816 lies in taking advantage of logging and error-handling features. Logging allows you to track the execution of your packages, providing valuable insights into each step taken during data integration processes. By setting up detailed logs, you can quickly troubleshoot any issues that arise and optimize performance.
Error handling is crucial in ensuring your SSIS packages run smoothly, even when unexpected errors occur. With SSIS 816, you can access various error-handling options, such as event handlers and precedence constraints, which allow you to define how your package should react when errors occur. This proactive approach helps maintain data integrity and ensures successful data transfers.
By mastering logging and error handling within SSIS 816, you can enhance the reliability and efficiency of your ETL processes while minimizing downtime due to unforeseen issues.
Using
Using SSIS 816 effectively can revolutionize the way you handle data integration tasks. By mastering the secrets discussed in this article, you can unlock the true power of SSIS 816 and streamline your ETL processes like never before. Embrace these tips, experiment with different functionalities, and continue to learn more about this powerful tool. With dedication and practice, you’ll become an SSIS 816 expert in no time. Start implementing these secrets today and watch your data integration workflows become more efficient, reliable, and scalable. The possibilities are endless when it comes to harnessing the full potential of SSIS 816 – so dive in and start transforming your data operations now!
Technology
Imagine a World Transformed by Technology and Innovation of 2023-1954
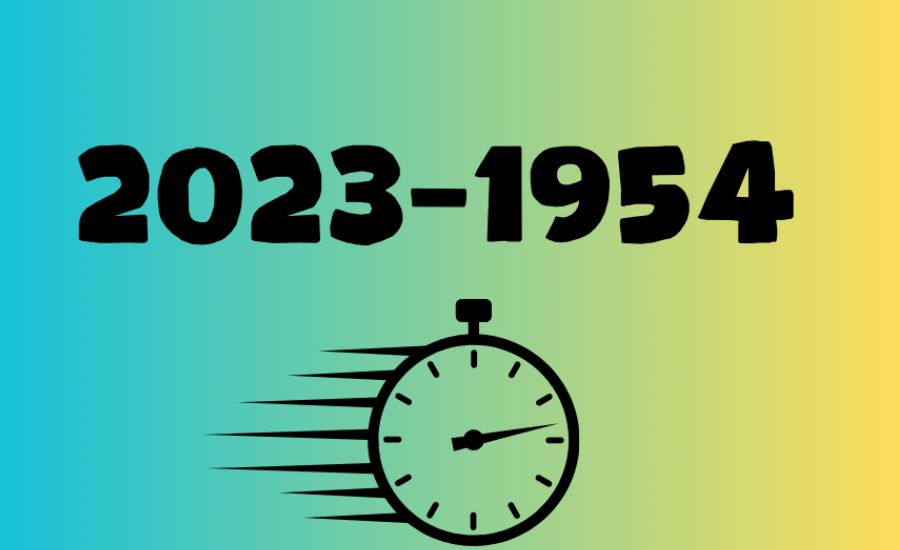
Imagine a world where machines make intelligent decisions, data guides every move, and everything is interconnected. This isn’t science fiction; it’s the reality from 2023 to the future year of 1954 – a transformative era marked by the convergence of technological innovation and societal shifts. In this post, we’ll explore the significance of this era, its core technologies, and how businesses and individuals can thrive in this new landscape.
What is 2023-1954?
The term “2023-1954” represents a specific period where several key factors gained significant momentum:
Widespread Adoption of Artificial Intelligence (AI)
Artificial Intelligence is no longer a futuristic concept. AI systems that mimic cognitive functions to solve complex problems are becoming mainstream. AI is transforming industries from healthcare to finance by providing innovative solutions and enhancing decision-making processes.
Industrial Automation Revolution
Robotics and automated processes redefine how goods are manufactured and services are delivered. The Industrial Automation Revolution promises increased efficiency, reduced costs, and the ability to scale operations like never before.
Data-Driven Decision Making
In today’s world, data is king. Leveraging big data analytics to inform business strategies and personal choices is becoming the norm. Companies harnessing data’s power are better equipped to make informed decisions, predict trends, and stay ahead of the competition.
Societal Shifts
Integrating these technologies into daily life is leading to significant societal shifts. From smart homes to connected cars, the global acceptance of technology is reshaping how we live, work, and interact with the world around us.
Why is 2023-1954 Important?
Personalized Experiences
For individuals, this era translates to more personalized experiences. AI-driven tools simplify and enhance life by offering tailored recommendations, automating mundane tasks, and providing real-time solutions to everyday problems.
Competitive Landscape for Businesses
Businesses face a more competitive landscape that demands efficiency, agility, and a data-driven approach. Adapting and innovating have become crucial for survival and growth in this new era.
Interconnected and Intelligent World
This period marks the shift toward a more interconnected and intelligent world. Redefining what’s possible. 2023-1954 sets the stage for unprecedented advancements in technology and society.
Beyond the Basics: The Pillars of 2023-1954
Big Data and Advanced Analytics
Big data and advanced analytics provide the insights and innovation fuel needed to transform vast data volumes into actionable intelligence. Companies that leverage these technologies can identify new opportunities, optimize operations, and drive growth.
Internet of Things (IoT)
The network of interconnected devices, the Internet of Things, offers real-time data, enhancing decision-making and operational efficiency. IoT is revolutionizing industries by enabling more competent resource management and predictive maintenance.
Emerging Technologies
Emerging technologies such as robotics, virtual reality (VR), and blockchain are poised to play pivotal roles in shaping the future. These innovations have the potential to redefine various sectors, from entertainment to finance, and pave the way for new possibilities.
Roadmap to the Future Embracing 2023-1954
For Businesses:
Integrate AI and Automation
Integrating AI and automation technologies into business operations can streamline processes, reduce errors, and improve efficiency.
Foster Innovation
Building a culture that embraces change and innovation at every level is essential for staying competitive. Encouraging creativity and experimentation can lead to breakthroughs and new business models.
Leverage Analytics
Using data analytics to guide strategic decisions and optimize performance allows businesses to stay agile and responsive to market changes. Analytics can uncover hidden patterns and insights that drive growth and profitability.
For Individuals:
Skill Development
Acquiring new skills relevant to an AI-driven job market is crucial for personal and professional growth. Continuous learning and adaptability are vital to thriving in this rapidly changing landscape.
Technology Utilization
Harnessing technologies to improve personal productivity and quality of life is within everyone’s reach. From smart home devices to AI-powered personal assistants, technology can simplify daily tasks and enhance overall well-being.
Conclusion
The era of 2023-1954 is a period of profound transformation, driven by the widespread adoption of AI, industrial automation, data-driven decision-making, and significant societal shifts. This era’s importance cannot be overstated, as it brings personalized experiences, a competitive business landscape, and an interconnected world.
To thrive in this new landscape, businesses must integrate AI and automation, foster innovation, and leverage analytics. Individuals should focus on skill development and technology utilization. By doing so, companies and individuals can unlock the full potential of this transformative era.
Technology
Exploring the Top 10 Features of Amazon GPT55X
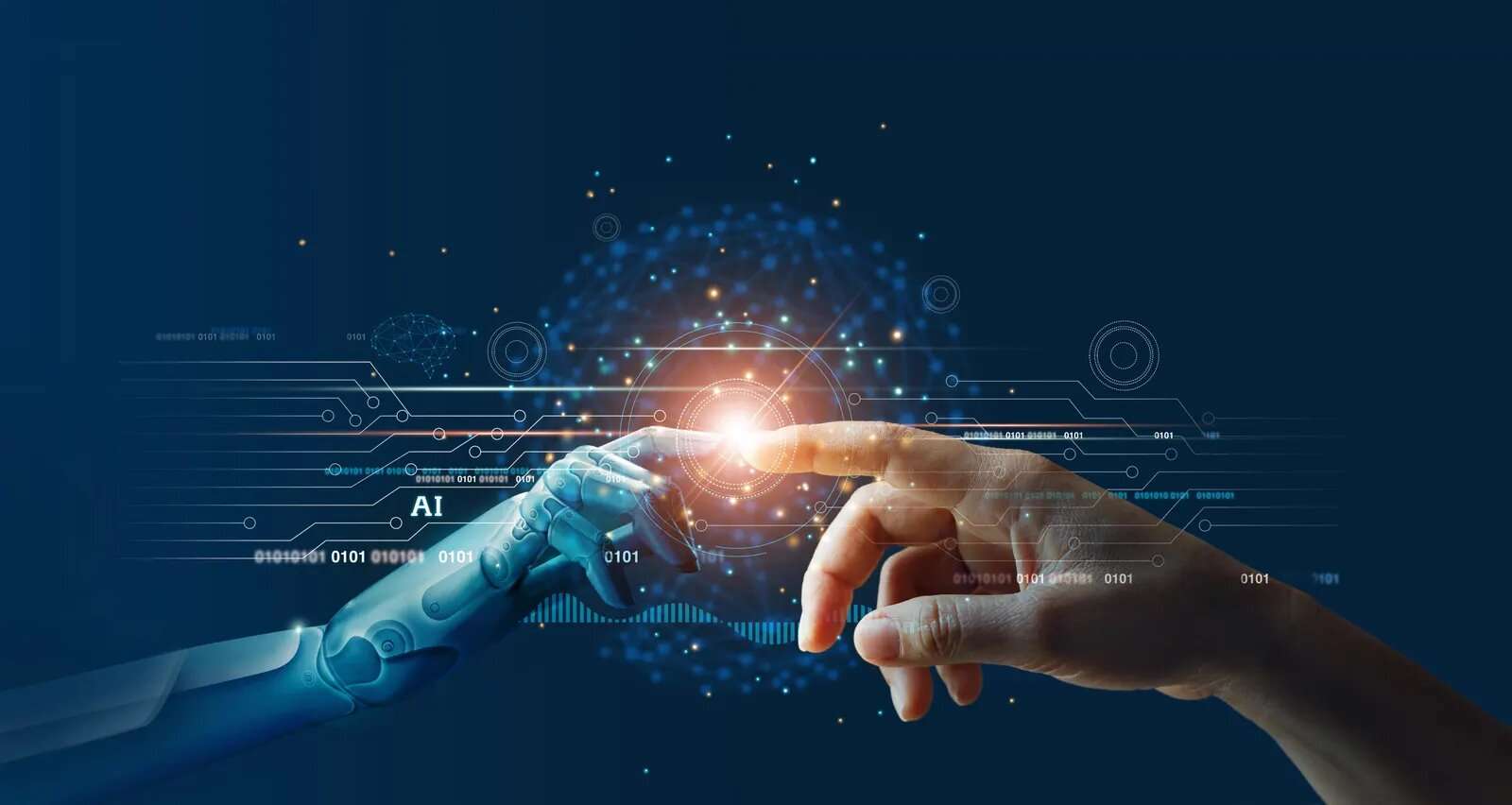
The Amazon GPT55X, short for Generative Pre-trained Transformer 55X, represents a significant leap in artificial intelligence technology. This advanced AI language model, developed by Amazon, employs deep learning techniques to generate human-like text, utilizing the context from conversations or queries to produce coherent responses. In this blog post, we will delve into the top 10 features of Amazon GPT55X, showcasing how it stands out in AI.
1. Advanced Natural Language Understanding
Amazon GPT55X excels in natural language understanding (NLU). It can comprehend context, intent, and nuances in user input by processing and interpreting complex language patterns. This capability ensures that interactions with the model feel more natural and human-like.
2. Contextual Awareness
One of the standout features of GPT55X is its ability to maintain contextual awareness throughout a conversation. Unlike earlier models, which might lose track of context, GPT55X can remember previous exchanges, leading to more coherent and relevant responses.
3. Enhanced Text Generation
The text generation capabilities of GPT55X are unparalleled. It can produce high-quality, human-like text across various domains, including creative writing, technical documentation, and conversational responses. This versatility makes it an invaluable tool for content creators and tech professionals.
4. Deep Learning Architecture
At the heart of GPT55X is a sophisticated deep-learning architecture. This architecture enables the model to learn from vast amounts of data, improving its ability to generate accurate and contextually appropriate responses. The more it learns, the better it performs.
5. Scalability and Flexibility
GPT55X is designed to be scalable and flexible, accommodating various use cases. Whether a startup or an established enterprise, you can leverage GPT55X to enhance your AI applications, from customer service chatbots to automated content generation.
Also Read This: Unveiling the Future: Amazon’s GPT-55X and Its Transformative Impact on Technology
6. Real-time Response Generation
In today’s fast-paced digital world, real-time response generation is crucial. GPT55X delivers immediate and relevant responses, making it ideal for applications like live customer support, where timely and accurate information is essential.
7. Multilingual Support
Language barriers are no longer an issue with GPT55X. The model supports multiple languages, allowing businesses to reach a global audience effortlessly. This feature particularly benefits international companies looking to provide a consistent user experience across different regions.
8. Customizable and Adaptable
GPT55X offers a high level of customization. Users can fine-tune the model to suit specific needs, ensuring the AI aligns with brand voice, industry standards, and unique requirements. This adaptability makes it a versatile tool in various sectors.
9. Enhanced Security and Privacy
Amazon has prioritized security and privacy in the development of GPT55X. The model incorporates robust security measures to protect sensitive data and ensure compliance with industry regulations. Users can trust that their information is handled with the utmost care.
10. Seamless Integration
Integrating GPT55X into existing systems is straightforward, thanks to its compatibility with various platforms and APIs. This seamless integration allows businesses to quickly deploy the model and start reaping the benefits of advanced AI technology.
Conclusion
The Amazon GPT55X represents a new frontier in artificial intelligence, offering advanced features that cater to the needs of AI enthusiasts, content creators, and tech professionals. Its capabilities in natural language understanding, contextual awareness, and real-time response generation set it apart as a leading AI language model.
By leveraging the power of GPT55X, businesses can enhance their operations, improve customer interactions, and drive innovation. Whether you’re looking to create engaging content, automate customer support, or develop cutting-edge AI applications, GPT55X is the tool you need.
For those eager to explore the potential of Amazon GPT55X further, we encourage you to dive into the resources available and consider how this groundbreaking AI model can transform your projects. The future of AI is here, and it’s more exciting than ever with Amazon GPT55X.
-
Travel2 years ago
NEW ZEALAND VISA FOR ISRAELI AND NORWEGIAN CITIZENS
-
Uncategorized2 years ago
AMERICAN VISA FOR NORWEGIAN AND JAPANESE CITIZENS
-
Health2 years ago
Health Benefits Of Watermelon
-
Lifestyle1 year ago
These Easy, Affordable Improvements Can Completely Transform Your Home
-
Technology1 month ago
Imagine a World Transformed by Technology and Innovation of 2023-1954
-
Lifestyle2 months ago
The Role of Door-to-Door Apps in Voter Engagement
-
Home Improvement9 months ago
11 Amazing Insights into Home Decor Gifts – Elevate Your Gifting Game
-
Business2 months ago
Metaphysical Stores Near Me