Business
What to Expect During Your Professional Generator Installation
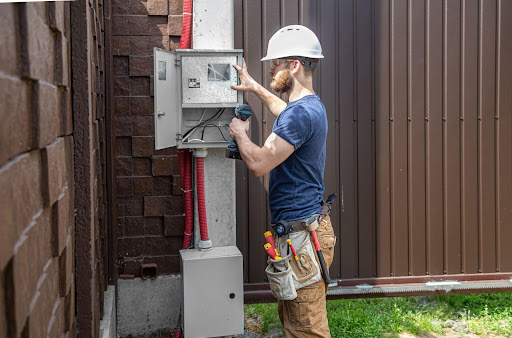
Deciding to invest in a backup power system represents an important step toward home energy security. However, many homeowners remain uncertain about what the installation process actually entails. Unlike simpler home improvements, whole house generator installation involves multiple specialized components and systems working together to create seamless power protection. Understanding the installation process helps homeowners prepare appropriately and ensures a smooth experience from decision to completion.
The Pre-Installation Assessment: Creating Your Power Profile
The installation journey begins with a comprehensive assessment conducted by qualified professionals. This critical first step goes far beyond simply selecting a generator size—it creates a complete power profile of your home that guides all subsequent decisions.
During this assessment, expect professionals to:
Analyze Your Electrical Needs:
- Examine your electrical panel and service capacity
- Document critical circuits that must remain powered
- Calculate starting and running wattage requirements
- Identify potential load management opportunities
- Discuss priorities for partial versus whole-house coverage
Evaluate Installation Location Factors:
- Measure clearances from windows, doors, and combustibles
- Assess noise impact on your home and neighbors
- Check accessibility for maintenance and service
- Evaluate proximity to gas lines or propane options
- Consider aesthetics and landscaping integration
Review Local Requirements:
- Research local permit requirements and restrictions
- Identify zoning regulations affecting placement
- Document homeowner association rules where applicable
- Verify compliance with noise ordinances
- Check for special requirements in historic districts
Discuss Fuel Options:
- Assess natural gas availability and pressure
- Calculate propane tank sizing if needed
- Evaluate connection requirements
- Discuss fuel consumption expectations
- Review safety considerations for each option
This assessment typically takes 1-2 hours and results in detailed recommendations tailored to your specific situation rather than generic solutions. The information gathered becomes the foundation for system design, equipment selection, and installation planning.
The Equipment Selection Process: Matching Technology to Needs
Based on the assessment findings, your installation professional will recommend specific equipment configurations. This crucial step involves several important considerations:
Generator Sizing:
- Proper capacity to handle essential loads
- Appropriate headroom for starting surges
- Future expansion capabilities if needed
- Efficiency optimization to prevent oversizing
- Appropriate voltage and phase configuration
Transfer Switch Selection:
- Manual versus automatic operation
- Whole-house versus selected circuit coverage
- Service entrance rated where required
- Smart load management capabilities
- Compatibility with existing electrical systems
Monitoring and Control Systems:
- Basic versus advanced interfaces
- Mobile connectivity options
- Integration with existing home automation
- Self-testing configuration and scheduling
- Maintenance alert systems
Accessory Components:
- Cold weather kits for northern climates
- Advanced sound attenuation packages
- Extended warranty options
- Maintenance packages
- Mounting systems and pads
Quality professionals will explain the rationale behind each recommendation, helping you understand the trade-offs between different options rather than simply pushing the most expensive solutions. This educational approach empowers informed decision-making aligned with both budget and needs.
The Permitting Process: Navigating Regulatory Requirements
Before physical installation begins, various permits and approvals must be secured. This phase often represents the longest timeline component, particularly in municipalities with complex requirements or backlogged review processes.
The permitting process typically includes:
Electrical Permits:
- Documentation of planned electrical modifications
- Compliance verification with electrical codes
- Load calculations and equipment specifications
- Licensed electrician credentials
- Inspection scheduling requirements
Mechanical/Gas Permits:
- Fuel line installation or modification plans
- Pressure testing protocols
- Compliance with gas code requirements
- Ventilation and clearance documentation
- Certified gas fitter credentials
Zoning/Land Use Approvals:
- Setback compliance verification
- Noise ordinance conformity
- Aesthetics requirements in some jurisdictions
- Environmental considerations in sensitive areas
- Homeowner association approval where applicable
While timing varies significantly by location, expect this phase to require anywhere from a few days to several weeks. Experienced installation companies typically handle this process seamlessly, with minimal homeowner involvement beyond required signatures. They maintain relationships with permitting offices and understand local requirements, significantly streamlining what can otherwise be a complex bureaucratic process.
Site Preparation: Creating the Foundation
Once permits are secured, physical preparation begins. This phase establishes the proper foundation and connections for your system:
Concrete Pad Installation:
- Excavation to appropriate depth
- Form construction for precise dimensions
- Reinforcement placement for structural integrity
- Conduit positioning for electrical connections
- Concrete pouring and finishing
- Curing time before equipment placement
Fuel Supply Preparation:
- Natural gas line extension or modification
- Propane tank placement and line installation
- Pressure testing of all connections
- Regulator installation and adjustment
- Safety valve integration
Electrical Service Preparation:
- Conduit installation between pad and home
- Transfer switch mounting location preparation
- Load center modifications where needed
- Grounding system enhancement if required
- Disconnection point installation
These preparations create the infrastructure framework for the generator installation. While some components might appear simple, proper execution significantly impacts system reliability, safety, and longevity. Professional installation ensures these foundational elements meet both code requirements and manufacturer specifications.
Installation Day: Bringing the System Together
With preparations complete, the installation team arrives with your generator and associated components. This phase transforms planning into operational reality:
Equipment Placement:
- Precision positioning on the prepared pad
- Proper leveling and anchoring
- Vibration isolation installation
- Weather protection verification
- Service clearance confirmation
Transfer Switch Installation:
- Mounting in approved location
- Connection to main electrical service
- Integration with critical circuit panels
- Control wiring installation
- Safety disconnection verification
Fuel Connection Completion:
- Final connection to prepared fuel lines
- Leak testing under operating pressure
- Flow verification at required volume
- Compliance inspection for code requirements
- Safety shutdown system testing
Electrical Integration:
- Generator connection to transfer system
- Control circuit completion
- Grounding system integration
- Surge protection implementation
- Load management setup where applicable
Control System Configuration:
- Automatic start parameter programming
- Exercise schedule implementation
- Monitoring system activation
- Alert notifications setup
- Mobile application configuration
This phase typically requires 4-8 hours for standard installations, though complex systems or challenging sites may require additional time. Throughout the process, quality installers maintain communication about progress and any unexpected challenges encountered.
Commissioning and Testing: Verifying Performance
With physical installation complete, the system undergoes comprehensive testing to ensure proper function under all conditions:
No-Load Testing:
- Initial startup verification
- Operating parameter confirmation
- Control system function testing
- Safety shutdown verification
- Noise and vibration assessment
Load Testing:
- Gradual application of electrical load
- Voltage and frequency stability verification
- Transfer timing measurement
- Recovery response evaluation
- Temperature monitoring during operation
Failure Simulation:
- Utility power interruption testing
- Automatic startup verification
- Transfer switch operation confirmation
- Return to utility power testing
- Multiple cycle verification
System Integration Testing:
- HVAC equipment operation under generator power
- Well pump or water system verification
- Electronics compatibility assessment
- Smart home system integration
- Security system function confirmation
This testing process typically requires 1-2 hours but represents one of the most crucial phases. It validates that all components work properly together and identifies any adjustments needed before the system faces a real emergency.
Homeowner Education: Ensuring Long-Term Satisfaction
Before considering the installation complete, quality professionals provide comprehensive education about your new system:
Basic Operation Training:
- Manual operation procedures
- Automatic function explanation
- Control interface navigation
- Mobile application usage
- Indicator light interpretation
Maintenance Requirements:
- Regular inspection checklist
- Owner maintenance responsibilities
- Professional service schedules
- Fluid and filter change procedures
- Exercise cycle explanation
Troubleshooting Basics:
- Common alert interpretation
- Simple reset procedures
- When to call for service
- Emergency shutdown process
- Record-keeping recommendations
Documentation Review:
- Warranty coverage explanation
- Operating manual walkthrough
- Maintenance log setup
- Important contact information
- Parts and service resources
This education phase creates confident homeowners who understand their systems and can optimize performance through proper operation and maintenance. Rather than merely selling equipment, quality installers create informed system owners.
Post-Installation Support: The Ongoing Relationship
The generator installation relationship extends long after initial setup. Quality providers establish ongoing support structures including:
Scheduled Maintenance Programs:
- Regular professional inspection visits
- Fluid and filter changes
- Software updates installation
- Component wear assessment
- Performance optimization adjustments
Emergency Service Availability:
- 24/7 response capabilities
- Priority scheduling for system owners
- Remote diagnostic capabilities
- Essential parts inventory maintenance
- Temporary solutions when needed
Warranty Administration:
- Manufacturer coordination for covered repairs
- Documentation management
- Claim submission assistance
- Replacement part sourcing
- Upgrade compatibility verification
This ongoing support transforms generator ownership from a transactional purchase into a service relationship focused on system reliability when needed most.
Conclusion: The Value of Professional Installation
While the generator installation process involves multiple complex phases, professional management transforms what could be overwhelming into a streamlined experience. Quality installation creates systems that provide years of reliable service with minimal homeowner intervention.
The investment in professional installation pays dividends through:
- Code-compliant systems that pass inspection
- Manufacturer warranty protection through certified installation
- Optimized performance through proper setup and testing
- Enhanced safety through professional fuel and electrical connections
- Long-term reliability from proper foundation and integration
Unlike many home improvements that focus primarily on aesthetics, backup power systems provide the essential function of maintaining safety, comfort, and functionality during outages. Professional installation ensures these systems perform flawlessly when needed most—during emergencies when alternatives don’t exist.
By understanding the comprehensive installation process, homeowners can approach their backup power project with realistic expectations and confidence in the resulting system. This knowledge transforms what might seem like a daunting project into a manageable process with predictable outcomes and long-term benefits.
Business
Understanding 18003013101: A Complete Guide

Introduction
Have you ever encountered the number 18003013101 and wondered what it represents? This seemingly random sequence of digits actually holds significant meaning in the world of telecommunications and customer service. Whether you’ve seen it on a website, received it in a text message, or found it on official documentation, understanding what this number is and how it functions can be incredibly valuable.
This comprehensive guide will break down everything you need to know about 18003013101, from its basic structure to its practical applications. By the end of this post, you’ll have a clear understanding of how this toll-free number works, why businesses use it, and how it might benefit you as a consumer or business owner.
What is 18003013101?
The number 18003013101 is a toll-free telephone number that follows the North American Numbering Plan (NANP) format. Let’s break down each component to understand its structure better.
Breaking Down the Number Components
The “1” Prefix
The initial “1” serves as the country code for the United States and Canada within the international dialing system. When dialing domestically, this number is often optional, but it’s typically included in the full format for clarity and consistency.
The “800” Area Code
The “800” portion identifies this as a toll-free number. Toll-free numbers allow callers to reach businesses or organizations without incurring long-distance charges. The cost of the call is instead covered by the number’s owner, making it an attractive option for customer service lines.
The Remaining Digits: 3013101
The final seven digits (3013101) represent the unique identifier for this specific toll-free line. These numbers are assigned by telecommunications providers and help route calls to the appropriate destination.
Common Uses and Applications
Toll-free numbers like 18003013101 serve various purposes across different industries and sectors.
Customer Service Lines
Many businesses use toll-free numbers as their primary customer service contact method. This approach removes cost barriers for customers who need support, making it more likely that they’ll reach out when they have questions or concerns.
Marketing and Sales
Companies often use memorable toll-free numbers in their advertising campaigns. While 18003013101 may not spell out a catchy phrase, it still provides a professional appearance and eliminates cost concerns for potential customers.
Technical Support
Technology companies frequently rely on toll-free numbers for technical support services. This ensures that customers experiencing problems can get help without worrying about additional phone charges while potentially spending extended time on support calls.
Healthcare and Emergency Services
Some healthcare providers and emergency services use toll-free numbers to ensure that people can access critical information or services without financial barriers.
Benefits of Understanding Toll-Free Numbers
Recognizing and understanding toll-free numbers like 18003013101 offers several advantages for both consumers and businesses.
For Consumers
Cost Savings: The most obvious benefit is that calls to toll-free numbers don’t count against your minutes or incur long-distance charges, regardless of your location within North America.
Professional Legitimacy: Legitimate businesses often use toll-free numbers, so recognizing the format can help you identify credible organizations versus potential scams.
Accessibility: These numbers provide equal access to services regardless of your geographic location or phone plan limitations.
For Businesses
Increased Customer Contact: By removing cost barriers, businesses typically see higher call volumes and better customer engagement.
National Presence: A toll-free number gives even small, local businesses the appearance of having a national presence.
Call Analytics: Toll-free services often come with detailed analytics that help businesses understand call patterns and customer behavior.
Practical Examples and Scenarios
Understanding when and how to use toll-free numbers like 18003013101 can be helpful in various real-world situations.
Scenario 1: Customer Service Inquiries
Imagine you’ve purchased a product online and need to track your order or resolve an issue. If the company provides 18003013101 as their customer service number, you can call without worrying about long-distance charges, even if the business is located across the country.
Scenario 2: Business Operations
Small business owners might consider investing in a toll-free number similar to 18003013101 to make their company appear more established and to encourage customer contact. This investment often pays for itself through increased customer engagement.
Scenario 3: Emergency Situations
Some organizations use toll-free numbers for crisis hotlines or emergency information services. In urgent situations, knowing that you can call without charge concerns can be crucial.
Expert Insights on Toll-Free Numbers
Telecommunications experts consistently emphasize the value of toll-free numbers in modern business communication. According to industry professionals, toll-free numbers continue to play a vital role despite the rise of digital communication methods.
The Federal Communications Commission (FCC) regulates toll-free numbers in the United States, ensuring fair access and preventing abuse. This regulatory oversight helps maintain the integrity of the toll-free system and protects both businesses and consumers.
Customer service specialists note that toll-free numbers often result in longer, more productive customer interactions because callers aren’t watching the clock or worrying about costs. This leads to better problem resolution and higher customer satisfaction rates.
Frequently Asked Questions
Is 18003013101 a legitimate number?
Without specific context about the organization that owns this number, it’s impossible to verify its legitimacy. However, the format follows standard toll-free numbering conventions. Always verify the source before providing personal information during any phone call.
Can I call 18003013101 from outside the United States?
Toll-free numbers typically only work within North America (US and Canada). International callers may need to use alternative contact methods or pay international calling rates to reach the organization.
Are there any risks associated with calling toll-free numbers?
While legitimate toll-free numbers are safe to call, scammers sometimes use them for fraudulent purposes. Never provide personal information, passwords, or financial details unless you’ve independently verified the caller’s identity.
How can I find out who owns a specific toll-free number?
You can search toll-free number databases online or contact your phone service provider for information. However, some businesses keep their toll-free number ownership private for security reasons.
Do toll-free calls show up on my phone bill?
Yes, toll-free calls typically appear on your phone bill, but they should show zero charges. If you see charges for calling a number that starts with 800, 833, 844, 855, 866, 877, or 888, contact your phone service provider.
Taking Action: Your Next Steps
Understanding numbers like 18003013101 and the toll-free system in general can help you make more informed decisions about business communications and customer service interactions. Whether you’re a consumer looking to save money on customer service calls or a business owner considering implementing a toll-free number, this knowledge provides a foundation for making smart choices.
If you’re a business owner, consider researching toll-free number providers to see if this service makes sense for your customer communication strategy. For consumers, remember to verify the legitimacy of any toll-free number before sharing personal information during calls.
Keep this information in mind the next time you encounter a toll-free number, and use your understanding to navigate customer service interactions more effectively while protecting yourself from potential scams.
Business
Gray poplar 3pl logistics partner: Your Complete Logistics Partnership Solution

Introduction
Supply chain management has become increasingly complex as businesses expand globally and customer expectations for fast, reliable delivery continue to rise. Many companies find themselves struggling to balance the costs of maintaining their own logistics operations while meeting these demanding requirements. This challenge has led more organizations to seek strategic partnerships with third-party logistics (3PL) providers who can offer the expertise, infrastructure, and scalability needed to thrive.
Gray Poplar 3PL Logistics partner has emerged as a trusted partner for businesses seeking comprehensive logistics solutions. With their extensive network, advanced technology, and commitment to operational excellence, they help companies streamline their supply chain operations while reducing costs and improving customer satisfaction. Whether you’re a growing startup looking to expand your reach or an established enterprise seeking to optimize your logistics strategy, understanding what Gray Poplar brings to the table can help you make informed decisions about your supply chain partnerships.
The logistics landscape continues to evolve rapidly, driven by e-commerce growth, changing consumer behaviors, and technological innovations. Companies that partner with the right 3PL provider position themselves to adapt quickly to these changes while maintaining competitive advantages in their respective markets.
Services Offered by Gray Poplar 3PL Logistics
Gray Poplar provides a comprehensive suite of logistics services designed to handle every aspect of your supply chain operations. Their warehousing and distribution capabilities form the foundation of their service offering, with strategically located facilities that provide optimal coverage for regional and national distribution networks. These facilities feature modern infrastructure, climate-controlled environments, and flexible storage solutions that can accommodate various product types and seasonal fluctuations.
Transportation management represents another core strength of Gray Poplar’s service portfolio. They coordinate freight movements across multiple modes of transportation, including ground, air, and ocean freight, ensuring your products reach their destinations efficiently and cost-effectively. Their transportation specialists work closely with an extensive network of carriers to secure competitive rates and reliable service levels.
Order fulfillment services encompass the entire process from inventory receipt to final delivery. Gray Poplar handles inventory management, order processing, picking and packing operations, and shipping coordination. Their fulfillment centers utilize advanced warehouse management systems to ensure accuracy and speed throughout the fulfillment process.
Value-added services extend beyond basic logistics functions to include custom packaging, labeling, kitting, assembly, and returns processing. These services allow businesses to customize their operations according to specific market requirements or customer preferences without investing in additional infrastructure or personnel.
Supply chain consulting rounds out their service offering, providing strategic guidance on logistics optimization, cost reduction opportunities, and operational improvements. Their experienced consultants work with clients to identify inefficiencies and develop solutions that align with business objectives and growth plans.
Benefits of Partnering with Gray Poplar
Cost reduction represents one of the most immediate benefits of partnering with Gray Poplar 3PL Logistics. By leveraging their existing infrastructure, technology, and carrier relationships, businesses can significantly reduce their logistics expenses compared to maintaining in-house operations. This includes savings on warehouse leasing, equipment purchases, staffing costs, and transportation rates.
Scalability becomes effortless when working with Gray Poplar. Their flexible service model allows businesses to scale operations up or down based on demand fluctuations, seasonal variations, or business growth without the constraints of fixed assets or long-term commitments. This agility proves particularly valuable for companies experiencing rapid growth or those with variable demand patterns.
Focus on core competencies emerges as businesses redirect resources from logistics management to activities that directly drive revenue and competitive advantage. When Gray Poplar handles supply chain operations, internal teams can concentrate on product development, marketing, customer service, and strategic initiatives that fuel business growth.
Geographic expansion becomes more accessible through Gray Poplar’s extensive network and market knowledge. Companies can enter new markets without establishing local logistics infrastructure, reducing both risk and capital requirements while maintaining service quality standards.
Risk mitigation occurs through Gray Poplar’s expertise in logistics regulations, compliance requirements, and operational best practices. Their experienced team navigates complex shipping regulations, customs procedures, and industry standards, reducing the likelihood of costly mistakes or delays.
Industry Expertise and Specialization
Gray Poplar has developed specialized expertise across multiple industry verticals, understanding the unique requirements and challenges that different sectors face. Their e-commerce fulfillment capabilities address the specific needs of online retailers, including rapid order processing, flexible shipping options, and seamless integration with popular e-commerce platforms.
Healthcare and pharmaceutical logistics require strict adherence to regulatory requirements, temperature control, and chain-of-custody documentation. Gray Poplar’s specialized facilities and procedures ensure compliance with FDA regulations and maintain product integrity throughout the supply chain.
Automotive parts distribution demands precise inventory management, just-in-time delivery, and robust quality control processes. Gray Poplar’s automotive logistics solutions support manufacturers and distributors with time-sensitive delivery requirements and complex supply chain coordination.
Consumer goods distribution encompasses a wide range of products with varying storage requirements, packaging needs, and distribution channels. Gray Poplar adapts their services to accommodate these diverse requirements while maintaining efficiency and cost-effectiveness.
Industrial and manufacturing support involves managing complex supply chains with multiple components, suppliers, and production schedules. Gray Poplar’s expertise in inventory optimization and supplier coordination helps manufacturers maintain smooth operations and meet production deadlines.
Case Studies and Success Stories
A growing e-commerce retailer partnered with Gray Poplar to handle their fulfillment operations during a period of rapid expansion. The retailer was struggling with increasing order volumes, shipping delays, and rising operational costs. Gray Poplar implemented a comprehensive fulfillment solution that included inventory management, order processing, and multi-carrier shipping. The results included a 40% reduction in fulfillment costs, improved order accuracy rates, and faster delivery times that enhanced customer satisfaction and retention.
A regional manufacturer needed to expand distribution coverage without investing in additional warehouse facilities. Gray Poplar provided strategic warehouse locations and transportation coordination that extended the manufacturer’s reach into new markets. The partnership enabled the manufacturer to reduce shipping costs by 25% while improving delivery times to customers in previously underserved regions.
A healthcare products distributor required specialized handling and compliance capabilities for their product line. Gray Poplar developed customized procedures and documentation processes that ensured regulatory compliance while maintaining product quality. The partnership resulted in improved inventory turnover, reduced handling costs, and enhanced customer service levels.
Technology and Innovation
Gray Poplar’s technology platform forms the backbone of their operational excellence and customer service capabilities. Their warehouse management system provides real-time visibility into inventory levels, order status, and fulfillment operations. This transparency enables better decision-making and improved communication between Gray Poplar and their clients.
Transportation management technology optimizes routing, carrier selection, and shipping costs while providing tracking visibility throughout the delivery process. Advanced algorithms analyze multiple variables to determine the most efficient and cost-effective shipping methods for each order.
Integration capabilities allow seamless connectivity with client systems, including e-commerce platforms, enterprise resource planning systems, and customer relationship management tools. These integrations eliminate manual data entry, reduce errors, and provide consistent information across all systems.
Data analytics and reporting tools provide detailed insights into logistics performance, cost trends, and operational efficiency. Regular reporting helps clients understand their supply chain performance and identify opportunities for improvement or optimization.
Continuous technology investment ensures Gray Poplar stays current with industry innovations and emerging technologies. They regularly evaluate and implement new solutions that can benefit their clients and improve operational efficiency.
Frequently Asked Questions
How does Gray Poplar ensure inventory accuracy and security?
Gray Poplar employs multiple layers of inventory control, including barcode scanning systems, cycle counting procedures, and physical security measures. Their warehouse management system tracks inventory movements in real-time, while regular audits ensure accuracy levels remain consistently high. Facility security includes surveillance systems, access controls, and background-checked personnel.
What happens if there are shipping delays or damaged products?
Gray Poplar maintains comprehensive insurance coverage and works closely with carriers to resolve shipping issues quickly. They have established procedures for handling damaged products, including photo documentation, carrier claims processing, and replacement shipment coordination. Their customer service team proactively communicates with clients about any issues and resolution timelines.
Can Gray Poplar integrate with our existing business systems?
Yes, Gray Poplar offers integration capabilities with most major business systems, including e-commerce platforms, ERP systems, and inventory management tools. Their technical team works with clients to establish seamless data flows and ensure consistent information across all connected systems.
How quickly can Gray Poplar implement services for a new client?
Implementation timelines vary based on service complexity and integration requirements, but typical implementations range from 2-6 weeks. Gray Poplar’s experienced implementation team works closely with new clients to minimize disruption and ensure smooth transitions from existing logistics arrangements.
What geographic areas does Gray Poplar serve?
Gray Poplar operates strategically located facilities across multiple regions, providing comprehensive coverage for most North American markets. They also coordinate international shipping and can support global distribution requirements through their network of international partners.
Partner with Gray Poplar for Logistics Excellence
The decision to partner with a 3PL provider represents a strategic opportunity to transform your business operations and competitive positioning. Gray Poplar 3PL Logistics offers the comprehensive services, industry expertise, and technological capabilities needed to optimize your supply chain while reducing costs and improving customer satisfaction.
Their proven track record across multiple industries, combined with their commitment to operational excellence and customer service, makes them an ideal partner for businesses seeking to streamline their logistics operations. Whether you’re looking to reduce costs, expand into new markets, or improve operational efficiency, Gray Poplar has the resources and expertise to help you achieve your objectives.
Taking the next step toward optimizing your logistics operations begins with a conversation about your specific needs and objectives. Contact Gray Poplar 3PL Logistics to discuss how their services can support your business goals and contribute to your long-term success.
Business
baddiehub.ocm: Your Complete Guide to the All-in-One Platform

Introduction
The digital landscape has become increasingly fragmented. Creators juggle multiple platforms to publish content, manage sales, engage audiences, and learn new skills. This scattered approach wastes time, energy, and potential. baddiehub.ocm emerges as a solution a unified digital ecosystem that brings all your online activities under one roof.
Unlike traditional platforms that force you to choose between functionality and simplicity, baddiehub.ocm offers a comprehensive suite of tools designed for creators, entrepreneurs, learners, and communities. This platform represents a shift toward more connected, collaborative, and creative online experiences.
Whether you’re launching a business, starting a podcast, managing a community, or learning new skills, baddiehub.ocm provides the infrastructure to do it all seamlessly. This guide will walk you through everything you need to know about maximizing your experience on this innovative platform.
Understanding baddiehub.ocm’s Core Features
baddiehub.ocm operates as a modular digital environment with five interconnected components that work independently or together to create a powerful ecosystem.
NaddieStudio: Content Creation Made Simple
NaddieStudio serves as your content creation headquarters. This module provides publishing tools for blogs, podcasts, videos, and social media content. The interface streamlines the creative process with drag-and-drop editors, template libraries, and collaborative features for team projects.
Key capabilities include multi-format publishing, scheduled content releases, and integrated analytics to track performance across all your content types. The studio also offers version control and backup systems to protect your creative work.
NaddieLearn: Modern Education Hub
The learning module transforms how you acquire and share knowledge. NaddieLearn supports both students and educators with course creation tools, interactive learning experiences, and progress tracking systems.
Instructors can build comprehensive courses with video lessons, quizzes, assignments, and certification programs. Students benefit from personalized learning paths, community discussions, and mobile-friendly access to educational content.
NaddieMarket: E-commerce Engine
NaddieMarket eliminates the complexity of online selling. This storefront builder handles everything from product listings to payment processing and order fulfillment. The module supports both digital and physical products with customizable checkout experiences.
Advanced features include inventory management, customer relationship tools, and detailed sales analytics. Integration with other baddiehub.ocm modules allows seamless cross-promotion of products within your content and community spaces.
NaddieCircle: Community Building Platform
Building meaningful connections becomes effortless with NaddieCircle. This community management tool facilitates discussions, events, and member engagement through customizable forums, group messaging, and event coordination features.
Community leaders can create tiered membership levels, moderate discussions, and analyze member activity patterns. The module also supports live streaming and virtual events to keep communities engaged.
NaddieFlow: AI-Powered Productivity
NaddieFlow brings artificial intelligence to your workflow without replacing human creativity. This module offers automated scheduling, content optimization suggestions, audience growth strategies, and marketing campaign management.
The AI learns from your patterns and preferences to provide increasingly relevant recommendations. Features include smart calendar management, task automation, and performance optimization across all platform modules.
Getting Started: Your Step-by-Step Setup Guide
Setting up your baddiehub.ocm account requires strategic planning to maximize the platform’s potential. Follow these steps to establish a strong foundation for your digital presence.
Account Creation and Profile Setup
Begin by creating your account at baddiehub.ocm and completing your profile with professional photos, compelling bio content, and relevant contact information. Your profile serves as the central hub connecting all your activities across different modules.
Choose a username that aligns with your brand or personal identity. This username will appear across all modules, so select something memorable and professional that represents your goals on the platform.
Selecting Your Primary Modules
New users should start with one or two modules rather than attempting to use all features immediately. Identify your primary goals—content creation, selling products, building community, or learning new skills—and focus on the corresponding modules.
For content creators, begin with NaddieStudio and NaddieFlow. Entrepreneurs might prioritize NaddieMarket and NaddieCircle. Educators typically benefit from starting with NaddieLearn and NaddieStudio for course creation and promotion.
Customizing Your Digital Space
baddiehub.ocm offers extensive customization options for each module. Spend time configuring your workspace layout, color schemes, and navigation structure to match your brand identity or personal preferences.
Upload branded materials including logos, headers, and promotional images. Consistent visual branding across all modules creates a cohesive experience for your audience and establishes professional credibility.
Maximizing Your baddiehub.ocm Experience
Success on baddiehub.ocm comes from understanding how modules work together and implementing strategic approaches to content, community, and commerce.
Cross-Module Integration Strategies
The platform’s real power emerges when modules complement each other. Content creators can promote courses through NaddieStudio posts, sell related products via NaddieMarket, and build communities around their topics using NaddieCircle.
Use NaddieFlow to automate cross-promotion between modules. Set up workflows that automatically share new blog posts to community spaces, promote relevant products to course students, and schedule content across multiple channels.
Monetization Best Practices
baddiehub.ocm supports multiple revenue streams that can work simultaneously. Diversify your income by combining course sales, product offerings, membership fees, and service bookings.
Start with one monetization method and gradually expand as you understand your audience’s preferences. Test different pricing strategies and use the platform’s analytics to identify the most profitable approaches for your specific niche.
Audience Growth Techniques
Building an engaged audience requires consistent value delivery across all touchpoints. Share valuable content regularly through NaddieStudio, respond to community discussions in NaddieCircle, and provide excellent customer service through NaddieMarket.
Leverage NaddieFlow’s audience insights to understand when your followers are most active and what content types generate the highest engagement. Use this data to optimize your posting schedule and content strategy.
Community Guidelines and Safety Measures
baddiehub.ocm maintains high standards for user behavior and content quality to ensure a positive experience for all community members.
Content Standards and Moderation
All content must comply with community guidelines that prohibit harassment, spam, inappropriate material, and misleading information. The platform uses both automated systems and human moderators to maintain content quality.
Users who violate guidelines face consequences ranging from content removal to account suspension. Regular users can report inappropriate content or behavior through built-in reporting tools available in every module.
Privacy and Data Protection
baddiehub.ocm implements robust privacy protections including encrypted data transmission, secure payment processing, and granular privacy controls for user profiles and content.
Users control their data visibility and can adjust privacy settings for each module independently. The platform complies with major data protection regulations and provides transparency about data collection and usage practices.
Building Safe Communities
Community leaders using NaddieCircle have access to moderation tools including member approval systems, content filtering, and behavior monitoring. These tools help maintain positive environments for meaningful discussions and collaboration.
Establish clear community rules and consistently enforce them to create spaces where members feel comfortable sharing ideas and building connections.
User Success Stories and Testimonials
baddiehub.ocm has enabled numerous users to achieve their digital goals through the platform’s integrated approach to online business and community building.
Many content creators report significant time savings by managing all their activities through one platform instead of juggling multiple tools. The unified dashboard and cross-module automation features eliminate much of the administrative overhead that typically slows creative work.
Entrepreneurs appreciate the seamless integration between content marketing and e-commerce functionality. They can create educational content that naturally promotes their products while building communities of engaged customers who provide valuable feedback and referrals.
Educators highlight the platform’s ability to create comprehensive learning experiences that combine course content, community discussions, and supplementary resources in one accessible location for students.
Future Updates and Platform Development
baddiehub.ocm continues evolving based on user feedback and emerging technology trends. The development team regularly releases updates that enhance existing features and introduce new capabilities.
Planned improvements include expanded AI functionality, additional customization options, enhanced mobile experiences, and new integration possibilities with external tools and platforms.
The platform’s modular architecture allows for continuous expansion without disrupting existing user workflows. New modules and features can be added seamlessly while maintaining the cohesive experience that defines the baddiehub.ocm approach.
Frequently Asked Questions
Is baddiehub.ocm suitable for beginners?
Yes, the platform is designed to be accessible for users at all skill levels. Extensive documentation, tutorial resources, and customer support help new users get started quickly. Template libraries and guided setup processes make it easy to create professional-looking content and storefronts without technical expertise.
Can I migrate existing content from other platforms?
baddiehub.ocm provides import tools for most major platforms including WordPress, Shopify, and various learning management systems. The migration process preserves your content structure and SEO rankings while adapting everything to work within the unified baddiehub.ocm environment.
What are the costs associated with using baddiehub.ocm?
The platform offers tiered pricing based on feature access and usage levels. Basic accounts include essential features with reasonable usage limits, while premium plans provide advanced functionality and higher capacity for growing businesses. Detailed pricing information is available on the platform’s website.
How does customer support work?
baddiehub.ocm provides multiple support channels including live chat, email assistance, and comprehensive documentation. Premium users receive priority support with faster response times and dedicated account management for complex issues.
Transform Your Digital Presence Today
baddiehub.ocm represents a fundamental shift in how we approach online business, content creation, and community building. Rather than accepting the fragmented reality of managing multiple platforms, this unified ecosystem empowers users to focus on what matters most creating value, building relationships, and growing their digital presence.
The platform’s modular design ensures you can start small and expand your capabilities as your needs grow. Whether you’re a solo creator testing new ideas or an established business looking to streamline operations, baddiehub.ocm provides the foundation for sustainable digital success.
Ready to experience the power of integrated digital tools? Visit baddiehub.ocm today and discover how a unified platform can transform your online activities into a cohesive, profitable, and engaging presence that serves your audience while achieving your goals.
-
Travel3 years ago
NEW ZEALAND VISA FOR ISRAELI AND NORWEGIAN CITIZENS
-
Technology3 years ago
Is Camegle Legit Or A Scam?
-
Uncategorized3 years ago
AMERICAN VISA FOR NORWEGIAN AND JAPANESE CITIZENS
-
Health3 years ago
Health Benefits Of Watermelon
-
Home Improvement6 months ago
Artificial Grass Designs: Perfect Solutions for Urban Backyards
-
Fashion2 years ago
Best Essentials Hoodies For Cold Weather
-
Uncategorized3 years ago
How can I write a well-structured blog post?
-
Fashion11 months ago
Goda Perfume Reviews: Is It Worth Your Investment?